Dust Collection or Dust Suppression: Which Approach Is Right for Your Facility?
The pros and cons of each fertilizer dust control method
In 2012, a study published in the journal Environmental Technology examined the impacts of fertilizer contamination from a phosphate plant on the east Mediterranean coast. Due to local wind conditions, fertilizer dust spread across untreated areas, leading to soil pollution and creating potential hazards for groundwater sources and plant life (Kassier, Lartiges, and Ouaini, 2012)[1]. This is just one example of what can happen when facilities fail to institute proper fertilizer dust control procedures. Not only can dust control help prevent harmful environmental effects, but it can also reduce hazards for workers and equipment.
The problems caused by fertilizer dust
A lack of fertilizer dust control leads to complications in four key areas: environmental impact, human health hazards, equipment breakdown, and dust-related explosions.
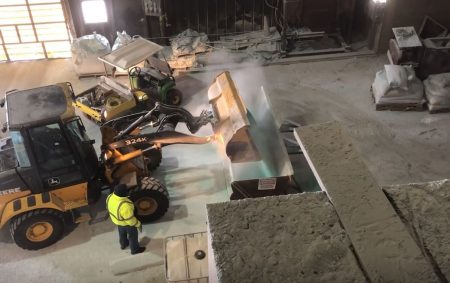
Unchecked dust in fertilizer processing facilities can lead to many issues.
As mentioned above, fertilizer contamination can negatively impact the environment. It depletes soil quality and kills off both plant and aquatic wildlife. This can potentially cause a shortage of fish, fauna, and flora, and it can lead to imbalances in the food chain, which can have far-reaching implications for food availability in local communities (Environment, 2015)[2].
Inside facilities, fertilizer dust can cause serious air quality issues. Constant inhalation of toxic particles has wide-ranging effects but includes acute symptoms like nausea, vomiting, skin irritation, and chemical pneumonitis (RoboVent, 2019)[3], as well as chronic diseases like cancer and asthma.
Fertilizer dust can also coat, jam, and corrode equipment, which leads to more frequent upkeep or premature replacements. And, the uncontrolled dust can mix with other chemicals, resulting in deadly dust combustion explosions (Lallanilla, 2013)[4].
Additionally, fertilizer dust can cause two major logistical headaches for production facilities. The presence of fertilizer dust means product waste; wasted product can indicate reduced product quality. There’s also reduced efficacy; a weakened product will perform poorly, and this could mean lackluster results for the end user, which means low crop yields and eventually a loss in sales.
So it’s clear, fertilizer dust control is a necessity. But when it comes to choosing the best approach, which one is right for your business?
Dust collection
Dust collection involves using a system or machine to capture and dispose of fertilizer dust.
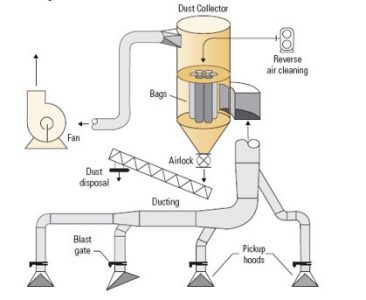
Example of a dust collection system
There are four primary types:
Exhaust hoods
Exhaust hoods are industrial versions of the hoods you find in residential home kitchens. Once activated, exhaust hoods capture dust at a velocity that’s strong enough to pull the dust away from its usual trajectory. Instead of blowing over workers or equipment, the dust is sucked into the hood. These hoods are typically built to the specific needs of each facility, and installation of these systems requires a deep understanding of airflow concepts, such as capture velocity, transport velocity, and dust distance.
Duct system
A duct system works more like a vacuum. It’s similar in appearance to the kind of duct system you’d find in a home or office building but it works at a superior level. It’s based around either a flexible hose or a hard, fixed hose. Flexible hoses are best for smaller facilities; hard, fixed duct systems are better suited for large ones. Duct systems suck the contaminated air out of the building and pump clean air back into the space.
Fan/motor system
Fan/motor systems are commonly referred to as high-pressure blowers. These machines come in a variety of sizes and blow the fertilizer dust away before it affects air quality.
Dust collectors
There are four different types of dust collector units on the market:
- Inertial separators: These units use centrifugal, gravitational, and inertial forces to remove fine dust particles that are suspended in air. Inertial separators can remove dust from gas as well.
- Fabric filters: These units are commonly used and come in many sizes. They filter dust and particulates from air or gas streams, but usually work as one component of a larger dust collection system.
- Wet scrubbers: These units use water to scrub dust particles from airstreams; they’re effective at reducing explosion potential.
- Electrostatic precipitators: These units use electrostatic force to pull in particle-polluted air. Then, they clean the air and pump out a clean airstream. Electrostatic precipitators are composed of several elements, including a power supply, ionizing source, dust removal component, and an external enclosure.
Dust collection safety and efficacy
Though dust collection is popular and can be effective, it’s not always safe. In 2015, the U.S. Chemical Safety Board found that, due to poor design and a frequent failure to test, dust collectors contributed to a high number of serious accidents (CSB, 2015)[5]. One such incident, a 2012 flash fire at a New Jersey plant, was caused by a dust collection system design failure; the system had only been in use for four days.
Concerning efficacy, there is no universally accepted standard for measuring industrial dust collector systems’ effectiveness. The most common rating is the American Society of Heating, Refrigerating and Air-Conditioning Engineers’ (ASHRAE) MERV standard (NAFA, 2018)[6]. However, this standard was established for the industrial ventilation cleaning industry, not the fertilizer industry.
Standard 199, an effectiveness test for dust cleaning collectors and filters, was introduced in 2016 to combat the lack of regulation. But to date, compliance with Standard 199 is voluntary (Kreczmer, 2017)[7].
Pros and Cons of Dust Collection
Dust collection has its share of benefits:
- There is a wide array of design options to suit facility needs.
- These dust collection options are capable of fine particle separation, they provide ventilation of heat and fumes, and the most effective designs achieve HEPA-quality filtration. (HEPA filters capture 99.97% of particles that are 0.3 microns.)
- Some NFPA-compliant dust collection models are available to ensure safer handling of combustible dusts.
However, despite these benefits, there are quite a few downsides:
- Many of these dust collection options are engineering-intensive and require lengthy design and installation processes.
- Because of these extensive processes, there are high initial costs and high ongoing energy costs.
- These options require a large physical footprint, and they’re difficult to retrofit into existing facility processes.
- Dust collection equipment requires routine service and maintenance which is often not supplied by the manufacturer.
- Any changes to your facility’s process will require system design changes and operational changes.
- Most units on the market are not NFPA-compliant and are prone to combustible dust explosions.
- Once dust is collected, it must still be handled and disposed of properly.
Dust Suppression
In contrast to dust collection, there’s dust suppression. Instead of collecting and disposing of dust, dust suppression prevents dust in the initial stages. Where dust collection is reactive, dust suppression is more proactive.
Dust suppression requires the use of spray systems. Through these systems, spray nozzles are used to apply dust control agents directly to the fertilizers to prevent the dust from becoming airborne when being conveyed and transported. The coatings mix with the dust particles; then the dust particles agglomerate together which weighs them down so they are returned to the ground or to their material source. Depending on your facility operations, you may need to use dust suppression in conjunction with other prevention methods.
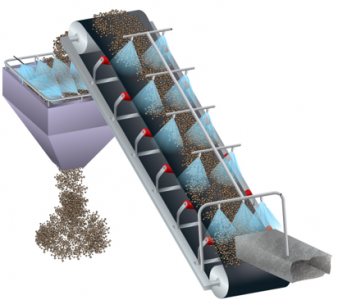
Example of a dust suppression system
There are four types of spray systems – water-only, water-based dust control agents, petroleum-based dust control agents, and with the introduction of MinTerra, a new line of coatings defined as synthetic dust control agents.
Water-only
Of the four spray system options available, a water-only system is the least effective. This system adds a lot of moisture, which compromises the quality of the fertilizer and disrupts material flow. There’s no physical barrier formed by use of water-only, there’s a poor coverage rate, and this product is prone to rapid drying. There’s also no ionic charge, and there’s only a short-term trapping of fine particulates, which means constant spraying. In fact, water-only spray systems have only shown an 80% effectiveness rate (Prostański, 2013)[8], which isn’t strong enough when product is on the line. Even if the amount of water used is restricted, adding moisture to the fertilizer begins to degrade the fertilizer before it makes it to the farmers’ fields, decreasing the overall yield and performance of the fertilizer. Any time moisture is added, it creates sticking and plugging of chutes and spreading equipment making it a material-handling nightmare. Not to mention, it can create a corrosive environment within the plant.
Water-based dust control agents
A water-based dust control system produces better results. This method adds very little moisture to the dry fertilizer but improves the wetting of fine particulates. There’s also a slight physical barrier. Water-based dust control agents and spray systems have an improved coverage rate, a slower drying time (which means longer dust control), cationic or anionic properties to attract dust particles, and short-term trapping of particulates. This method is best utilized when dust control is needed between the distributor and the fertilizer being spread in the field.
Petroleum-based dust control agents
Petroleum-based dust control agents are the best option for fertilizers used to date. They add no moisture, reducing their effect on product quality and material flow. They create a defined physical barrier and provide the best coverage rate. Petroleum-based dust control agents are highly resistant to drying, which means long-term trapping of fine particulates. As materials can be stored for months at a time before making it to the field to be applied, these agents are used in fertilizer manufacturing for long-term dust control. The key downside is most petroleum-based dust control agents require the product to be heated before being applied, which can add unnecessary costs and complicate manufacturing processes. In certain instances where a product requires heating before application, such as wax coatings, waxes can help maintain the integrity of the product and control dust up to a year once the wax creates a hardened shell on the fertilizer surface.
Synthetic dust control agents
Synthetic dust control agents are the latest technology for fertilizers coatings. MinTerra DustAid Synthetic products are leading the way in transforming how fertilizer dust control agents are used in the industry. Like petroleum-based dust control agents, synthetics add no moisture, so they have little effect on product quality and material flow. They, too, create a defined physical barrier, provide the best coverage rate, and are highly resistant to drying, making them ideal for fertilizers held in long-term storage. The distinct advantage of synthetic dust control agents over petroleum-based agents is they do NOT need to be heated before being applied. They can be transported, stored, and applied at room temperature. These products are low in viscosity, too, which simplifies the application system, requires fewer application points, but still provides long-term dust control, in many cases up to one year with a single application.
Pros and Cons of Spray Systems
Spray systems, in all varieties, have a slew of benefits:
- Dust is controlled, never airborne. It stays where it’s meant to be, which protects the quality of fertilizer products.
- There’s a low initial cost and low ongoing energy costs associated with application equipment.
- There’s a single application point.
- Service costs are included in the price of the system.
- There’s a small physical footprint since no extensive equipment installation is required; this is easy to retrofit into existing facility processes.
- Spray systems involve simple engineering, with a short design-fabricate-install-operate timeline.
- There’s a wide array of chemical options to treat all kinds of dust.
- Spray systems are highly effective, with a dust emissions reduction rate of 99% or higher.
There are a few negatives:
- The water and/or chemicals used in the spraying could damage process equipment or certain non-fertilizer materials.
- Water-based programs use high water volumes.
- There’s no service available for water-only programs.
- Chemical-based programs require storage and handling considerations, in addition to protocol already being followed for fertilizer.
When choosing a method for fertilizer dust control, it’s important to consider the needs of your product and facility. However, between dust collection and dust suppression, dust suppression offers the strongest results and is safer, more affordable, and easier to incorporate.
Explore our dust suppression and coating options under our MinTerra line. DustAid works with several types of fertilizer and is designed for effectiveness during the manufacturing, transportation, and application phases. Learn more about DustAid here: http://mintech.com/minterra/dustaid/.
[1] Kassir, Lina Nafeh, Lartiges, Bruno, and Ouaini, Naim. (2012). Effects of fertilizer industry emissions on local soil contamination: a case study of a phosphate plant on the east Mediterranean coast. Retrieved from: https://www.tandfonline.com/doi/abs/10.1080/09593330.2011.601765?journalCode=tent20
[2] Environment. (2015). How Do Fertilizers Affect the Environment. Retrieved from: https://www.environment.co.za/environmental-issues/how-do-fertilizers-affect-the-environment.html
[3] RoboVent. (2019). Fertilizer Dust Collection. Retrieved from: https://www.robovent.com/dust-collection/fertilizer-dust-collection/
[4] Lallanilla, Marc. (April 18, 2013). What Causes Fertilizer Explosions? Retrieved from: https://www.scientificamerican.com/article/what-causes-fertilizer-explosions/
[5] CSB. (January 15, 2015). CBS Names Poor Design and Failure to Test Dust Collection System Among Causes of U.S. Ink New Jersey Flash Fire that Burned Seven Workers in 2012. Retrieved from: https://www.csb.gov/csb-names-poor-design-and-failure-to-test-dust-collection-system-among-causes-of-us-ink-new-jersey-flash-fire-that-burned-seven-workers-in-2012-osha-again-urged-to-issue-new-combustible-dust-regulations-/
[6] NAFA. (October 2018). Understanding MERV. Retrieved from: https://www.nafahq.org/understanding-merv/
[7] Kreczmer, Rick. (November 1, 2017). ANSI/ASHRAE Standard 199 improves industrial dust collection. Retrieved from: https://www.ishn.com/articles/107521-ansiashrae-standard-199-improves-industrial-dust-collection
[8] Prostański, Dariusz. (2013). Use of Air-and-Water Spraying Systems for Improving Dust Control in Mines. Retrieved from: https://www.sciencedirect.com/science/article/pii/S2300396015300550