Dust Regulations Every Fertilizer Processor Should Know
Fertilizer dust control can save product and keep workers safe
Fertilizer manufacturers ultimately want to produce the best possible product – fertilizer with high production yields, high material integrity and quality, and strong marketability. But the manufacturing process leads to other concerns and challenges. Manufacturers must also reduce explosion potential in their facilities and reduce their workers’ exposure to toxins, which means pristine facility hygiene. All of these goals can be achieved through fertilizer dust control.
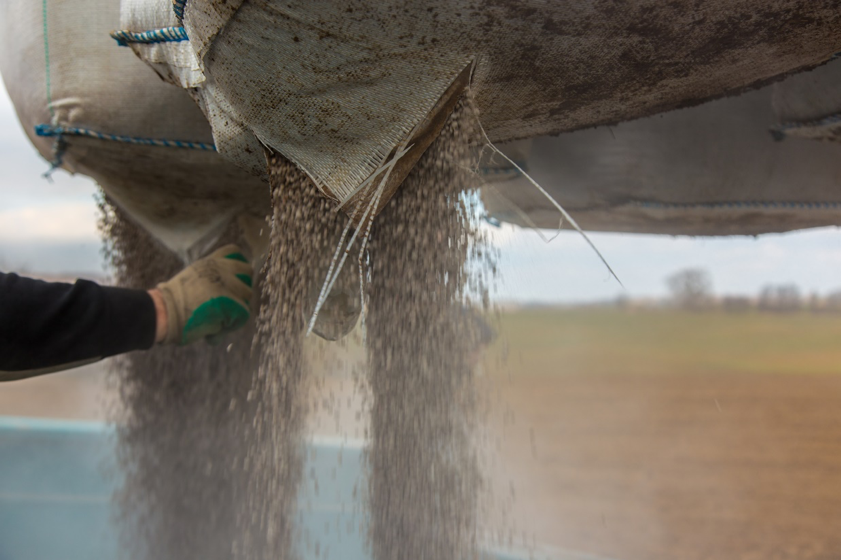
Dusting of fertilizer at various points in manufacturing, transporting, and storage can cause many issues from equipment wear to higher probability of explosions.
Why fertilizer dust control matters
Without dust control, the fertilizer manufacturer faces a lot of potential liability, danger for workers, and loss of product and equipment. Not to mention, fertilizer dust-related problems could cause damage to the manufacturer’s reputation within the industry.
On one end, a lack of fertilizer dust control can have minimal effects. A processing facility might need to invest in more frequent maintenance and upkeep of machinery or purchase new machinery more frequently. This means unnecessary expenditures when these funds could be used elsewhere in the business.
But a lack of dust control can have more detrimental effects. Prolonged, unmitigated exposure to toxins could result in illness or disease for workers. A study published in the American Journal of Industrial Medicine (Daniels, Dunn, Kubale, Stayner, & Yiin, 2016)[1]found that workers continuously exposed to various chemical elements at a phosphate fertilizer plant had higher rates of lung cancer and emphysema. Poor dust control can even lead to disaster. The 1947 Texas City, Texas blast was the deadliest industrial accident in American history (Lallanilla, 2013)[2], and it was caused by improper handling of ammonium nitrate, which is a key ingredient used to improve fertilizer’s nitrogen content. More recently, a 2013 fire at an ammonium nitrate storage and distribution facility in West, Texas killed 15 people (EPA, 2015)[3]and even damaged nearby businesses, homes, and schools.
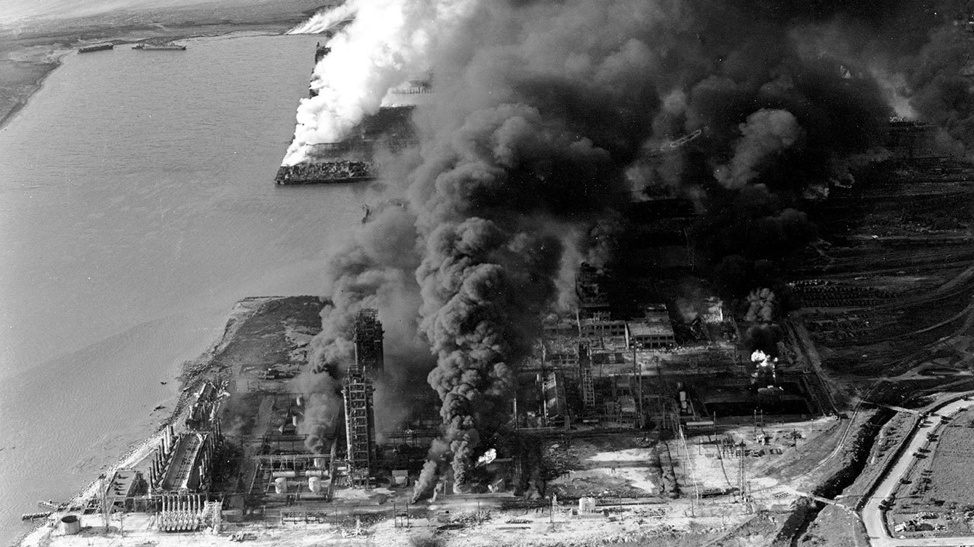
1947 Texas City, Texas explosion at an ammonium nitrate plant had blasts so strong they shattered windows 40 miles away in Houston.
Fertilizer dust control isn’t just a way for processing facilities to save money; it can also save lives.
The benefits of dust control
Dust that’s produced during material processing operations becomes a major source of harm and environmental pollution. This isn’t just in the processing facilities; it’s also a concern at the mining stage and even during shipping and storage.
Fertilizer dust control can mitigate risk at every stage of the production process:
- It protects granule integrity during storage.
- It ensures fertilizer doesn’t become too fragile, which prevents deterioration.
- It reduces risk of fire and dust explosion.
- It boosts safety for all workers and improves on-site visibility.
- It prevents unpleasant odors.
- It reduces the need for, and cost of, maintenance and cleaning.
- It slows wear and tear on equipment.
- It cuts down on wasted product.
- And, it creates a healthier workplace, which in turn improves worker morale and boosts both production and the quality of work.
Some facilities aren’t taking the proper actions, mistakenly thinking they can continue on business as usual or refine select parts of their production processes. But other companies have turned to regular dust control coatings because they’re long-lasting, they minimally impact the treated fertilizer’s flowability, and they make day-to-day operations safer and more economical. Even better, fertilizer dust control helps facilities and farmers alike ensure compliance with federal regulations.
Essential regulations for every fertilizer processor
In addition to worker safety and protecting the environment, dust control coatings help with compliance with a slew of regulations from the Environmental Protection Agency (EPA), Occupational Safety and Health Administration (OSHA), and Mine Safety and Health Administration (MSHA). There are several regulations, and it’s recommended that all fertilizer manufacturers and farmers read them in full, but some of the most important ones to note are as follows.
EPA
- For facilities that handle more than a threshold quantity of certain toxic and/or flammable substances, they’re required to have a Risk Management Program and Plan (RMP) in place. The RMP must be submitted to the EPA for approval. This plan covers everything from a prevention program and risk management plan to an emergency response program and plans for communication with the public in the event of an accident or emergency (EPA, 2019)[4].
- Each fertilizer facility and all farms must adhere to the General Duty Clause, which essentially states that any business handling hazardous chemicals has a duty to identify potential hazards and take steps to ensure safety for workers and surrounding communities (EPA, 2009).[5]
- Fertilizer facilities must follow the Emergency Planning and Community Right-to-Know Act (EPCRA), which was created in 1986 and requires facilities to report the storage and handling of hazardous materials to federal, state, and local governments (EPA, 2019)[6].
- Some farms are subject to the Clean Air Act, which monitors the release of certain pollutants into the environment and regulates air quality (EPA, 2019)[7].
- EPA also offers guidance and research specific to different types of fertilizer (EPA, 2019)[8]. For example, for fertilizers made from recycled wastes, there are limits for the amount of heavy metals or toxic compounds that can be included in these products.
OSHA
In conjunction with the EPA, OSHA has pulled together an exhaustive list of resources about handling fertilizer.
- There are several regulations about the safe storage, handling, and management of solid ammonium nitrate prills (EPA, OSHA, 2015)[9]. For example, AN prills can’t be heated in a confined space, they can’t be exposed to strong shock waves from explosives, and they can’t be contaminated with combustible materials or organic substances.
Concerning the storage of ammonium nitrate, OSHA goes deep into the innerworkings of processing facilities (OSHA, 2019)[10]:
- Floors must be constructed to eliminate floor drains and piping, to keep out molten materials that could flow or be confined during a fire.
- Facilities must regularly clean floors and equipment as well as the entire plant.
- The land surrounding a mixing plant must be kept clear of brush, dried grass, leaves, and other flammable shrubs for 25 feet.
- Facilities must dispose of AN bags in a safe manner.
- Explosives can’t be used inside of or within 50 feet of a facility that’s used for mixing blasting agents.
MSHA
MSHA focuses many regulations on the proper handling of hazardous chemicals and protection of workers doing the handling.
- Facilities must inform miners about chemical hazards. This involves inventorying chemicals at the mine, determining the hazardous ones, keeping an updated list, writing out a hazard program, and properly labeling hazardous chemicals with accurate Material Safety Data Sheets (MSHA, 2002).[11]
- The MINER Act requires Mine Emergency Response Development (MERD) exercises at least twice per year, to ensure that emergency plans are adequate and officials can act swiftly in the case of a real emergency (MSHA, 2009).[12]
- Mining companies are also obligated by law to maintain the lowest possible personal dust exposure limit for miners (MSHA, 2009).[13]
In short, fertilizer dust control is a necessary part of any fertilizer processing facility’s operations, as it helps company efficiency, ensures worker safety, and fosters the creation of a stronger product for farmers. The EPA, OSHA, and MSHA regulations further illustrate why dust control and proper handling of hazardous chemicals is so important.
If you’re not sure where to start with fertilizer dust control for your facility, look to DustAid from MinTech’s MinTerra product line. DustAid coatings were designed to control dust during manufacturing, transportation, and application stages, and they reduce dust on a wide variety of fertilizer blends. To find out more about DustAid, visit http://mintech.com/minterra/dustaid/.
[1]Daniels, R. D., Dunn, K. L., Kubale, T. L., Stayner, L. T., & Yiin, James H. (2016). A Study Update of Mortality in Workers at a Phosphate Fertilizer Production Facility. Retrieved from: https://www.ncbi.nlm.nih.gov/pmc/articles/PMC4913354/
[2]Lallanilla, Marc. (2013). What Causes Fertilizer Explosions?Retrieved from: https://www.scientificamerican.com/article/what-causes-fertilizer-explosions/
[3]Environmental Protection Agency. (2015). Chemical Advisory: Safe Storage, Handling, and Management of Solid Ammonium Nitrate Prills. Retrieved from: https://www.epa.gov/sites/production/files/2015-06/documents/an_advisory_6-5-15.pdf
[4]EPA. (2019) Risk Management Plan (RMP) Rule. Retrieved from: https://www.epa.gov/rmp
[5]EPA. (2009). The General Duty Clause. Retrieved from: https://www.epa.gov/sites/production/files/2013-10/documents/gdc-fact.pdf
[6]EPA .(2019). Emergency Planning and Community Right-to-Know Act (EPCRA). Retrieved from: https://www.epa.gov/epcra
[7]EPA. (2019). Summary of the Clean Air Act. Retrieved from: https://www.epa.gov/laws-regulations/summary-clean-air-act
[8]EPA. (2019). Agriculture Nutrient Management and Fertilizer. Retrieved from: https://www.epa.gov/agriculture/agriculture-nutrient-management-and-fertilizer
[9]EPA, OSHA. (2015). Chemical Advisory: Safe Storage, Handling, and Management of Solid Ammonium Nitrate Prills. Retrieved from: https://www.epa.gov/sites/production/files/2015-06/documents/an_advisory_6-5-15.pdf
[10]OSHA. (2019). 1910.109 – Explosives and blasting agents. Retrieved from: https://www.osha.gov/laws-regs/regulations/standardnumber/1910/1910.109
[11]MSHA. (2002). Telling Miners About Chemical Hazards. Retrieved from: https://arlweb.msha.gov/REGS/COMPLIAN/GUIDES/Hazcom/HazComToolKit.pdf
[12]MSHA (2009). Mine Emergency Response Development (MERD) Contest Guidelines. Retrieved from: https://arlweb.msha.gov/REGS/COMPLIAN/GUIDES/MERDGuidelines062009.pdf
[13]MSHA (2009). Questions and Answers, MSHA’s Final Rule on Conveyer Belt, Fire Prevention and Detection, and Use of Air From the Belt Entry. Retrieved from: https://arlweb.msha.gov/REGS/COMPLIAN/GUIDES/BeltAir.pdf