4 Reasons Foam Dust Control is Better For Coal Handling
Imagine what it is like to hike on a trail in the mountains during an early summer morning. The trail bends and winds alongside the mossy creek bed and you pause along the edge to breathe the fresh air and take in the beauty around you. The cool mountain air rushes into your lungs, and you feel refreshed and invigorated. There’s just something soothing about a breath of fresh air.
Now you’re transported to a coal-fired power plant. The conveyor bends and winds its way up from the coal pile to the crusher and ultimately the furnace. At each transfer point the dust flies, the air fills with fine coal particles, and the dust respirator you’re wearing itches and restricts your breathing. You long for that fresh mountain air.
When moving coal around, it is not easy keeping the coal dust particles from catching wind. Anyone who has worked with coal knows its potential for generating dust – dust that creates a hazard to safety and health. The brittle nature of coal, especially subbituminous coal, makes dust very difficult to control.
The United States EPA, OSHA, and MSHA have imposed regulations on facilities that handle coal, regulations designed to protect workers and the environment from this fugitive coal dust emission. Many techniques have been used to reduce coal dust emissions when moving coal around over the years, but there is still room for improvement.
As advanced as mining and power generation are, it is quite amazing that the most common method for controlling coal dust is still the outdated method of spraying the coal with water. This archaic practice is not only ineffective at controlling respirable dusts, it also creates many logistical problems that rob BTUs and dollars from the power generation process.
Adding high volumes of water to coal causes caking and plugging in chutes, hoppers, and silos. The addition of water also increases the propensity of coal to self-heat, starting the runaway process of spontaneous combustion. The most significant impact of adding water to coal is the reduction of heating capacity – the loss of BTUs.
The latest chemical technologies allow for a solution to coal dust that is not only more cost-effective than water, but also eliminates all of the negative side-effects of adding water: low moisture foam. It is safe, easy to create, simple to apply, and provides 95% reduction of respirable coal dust without affecting the BTUs, emissions, or infrastructure.
A little bit of foam goes a long way. As little as one tote of MinTech’s unique foaming agent can suppress the dust of 65,000 tons of coal. That equates to 550 rail cars of coal.
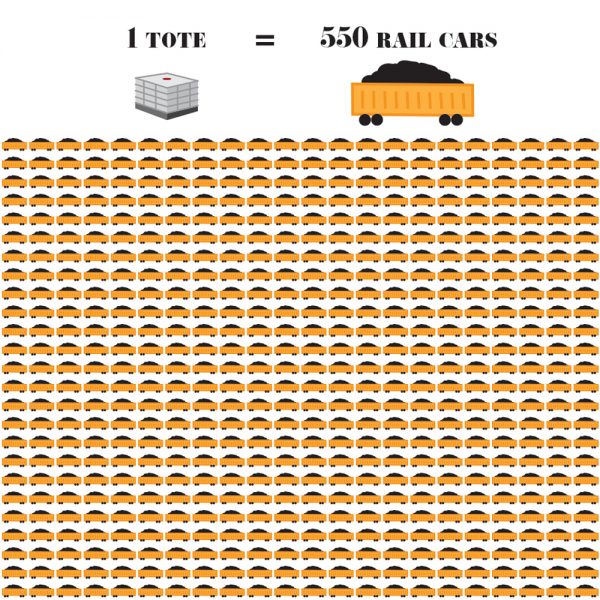
For those in the coal handling industry seeking alternatives to wetting coal with plain water, let’s discuss four reasons properly installed foam dust control systems might be better than what you have now.
1. SAVE YOUR BTUs
Coal already has inherent surface moisture which fluctuates throughout the handling process. Coal gains water naturally during transport, at terminals, and while sitting in stockpiles.
Water-based dust suppression systems can add anywhere from 20 – 40 pounds of additional moisture per ton of coal, which soaks up valuable heating content of the coal. Now you have to use your energy evaporating all the moisture you just added rather than creating more heat. What if you could burn coal, maintain the BTU value you paid for, while controlling dust along with way?
With foam dust control systems, you can typically use 10X less moisture and control dust greater than 95% better than water-only systems. Foam gives you the ability to keep the coal from massive gains in moisture which keeps the BTU value up allowing you to burn more coal rather than evaporate water.
This is achieved by mixing compressed air with unique foaming agents to deliver a dry-to-the-touch dust-encapsulating blanket of foam. This blanket of foam adheres instantly to the coal surface, trapping dust fines in a physical barrier while adhering them together with a chemical binding action.
2. WORK BETTER
You, your coworkers, equipment, pumps, and environment – all work better in cleaner, healthier, air. When everyone and everything breathes better, work can be performed safer and facilities operate more efficiently.
You avoid risking exposure to coal dust, which has been known to cause respiratory and cardiovascular illnesses such as black lung disease and arrhythmias.
You avoid regularly clogged filters, pump failures, deficiencies in equipment performance, shortened equipment life, and other failures.
You avoid harmful environmental effects – air pollution, reduced visibility, accelerated corrosion rates, increased water toxicity.
3. AVOID UNNECESSARY MAINTENANCE
Eliminating airborne dust with foam instead of water allows you to safely work and move coal around without causing:
- equipment failures
- corrosion to metal surfaces and infrastructure
- daily cleanups and wash-downs due to dust accumulation and spillage
Or worst case scenario, having to shut down the power plant to fix a preventable dust-related problem.
MinTech will custom-design a system and program to meet your specific challenges. Our technology not only eliminates fugitive dust emissions, but also solves all of the problems caused by water-only systems. The best part is that MinTech will install, operate, and maintain your dust control system for you. No need to add that to your growing list of daily maintenance projects. We will take care of the dust. You just take care of business.
4. SAVE WATER (AND MONEY)
Whether you are using on-site pond water, water from a lake or river, or municipal water sources, it costs money to water coal. It costs money to move water, to operate and maintain the water spray equipment, and to deal with the slippery mess that water creates.
A 2400 MW power plant running at full capacity can easily run 30,000 tons of coal per day. With a water-only dust control system, that plant would apply 53 million gallons of water per year to the coal, costing hundreds of thousands of dollars in lost energy. With a foam program, that same plant would need less than 3 million gallons of water, a savings of over 50 million gallons of water annually!
MinTech is challenging the status quo and proving that new technologies not only out-perform archaic water-only programs, but also provide significant savings, while improving safety to workers and environments. MinTech is your one-stop-shop for all your coal dust suppression needs. With our combined 300+ years of solving the coal industry’s material handling challenges, our team of chemists, engineers, and application experts are here as partners to work through these challenges.
Go ahead – contact us to schedule a free on-site assessment to start your journey to something much better than what you have now.